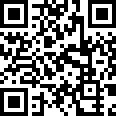
Ms. Fiona Cui
Leave a messageMs. Fiona Cui
Leave a message
1. History of Thermal Spraying
China's thermal spraying technology began in the 1950s, when Wu Jianchun and others in Shanghai set up the first domestic specialised spraying plant, the development of oxyacetylene flame wire spraying and electrospray device, and foreign metal spraying business.
In the 1960s, a few military units began to study plasma spraying technology (such as the Beijing Institute of Aeronautical Technology, Aerospace Corporation Rocket Technology Research Institute 703, aviation sector 410, 420, 430 plants and other units), began to be applied in China's military sector.
To the mid to late 70s appeared many varieties of oxyacetylene flame metal powder spraying (fusion) equipment and a variety of nickel, iron, cobalt-based self-melting alloy powder and composite powder coating materials, to the rapid forward development of thermal spraying technology has laid a solid foundation. Thermal spraying materials are thermal spraying technology, "cooking food", the increase in the variety of materials and performance improvement will directly improve the quality of the coating.
In machinery, metallurgy, petrochemical, electric power, railway, paper, textile, medical and health, military and national defence and many other sectors of the national economy has been widely used. In the 1990s to a new stage of development, the development of this stage is characterized by: equipment to high-energy, high enthalpy, high-speed direction; materials to the series, standardization, commercialization direction to ensure that multi-functional high-quality coating needs; process technology to the direction of mechanization, automation, such as computer control, mechanical operation, and so on.
2. Application status of thermal spraying technology
Thermal spraying technology as a technology involving a wide range of processing technology is relatively simple and flexible, a wide range of applications, economic benefits of the new modern processing technology, which can make the surface with wear-resistant, corrosion-resistant, adiabatic, heat-resistant, electrically conductive, insulating, anti-erosion, oxidation-resistant, friction-reducing, lubrication, radiation protection and other functions. Not only can be used for mechanical parts of the repair and surface strengthening, but also can be used for manufacturing.
Due to the wide range of choice of spraying materials, not subject to the overall material alloying restrictions, can be more convenient to obtain super-hard alloys, a variety of ceramic or metal-ceramic coatings as well as a variety of functional coatings, and coatings relative to the overall high-level material for the amount of material is less than the overall improvement of the material is undoubtedly much more economical, and therefore can be boldly used in the use of valuable materials, its cost will not increase a lot, while the surface performance of the material can be obtained The cost will not increase much, but the surface performance of the material can be greatly improved, the service life of the parts repaired by thermal spraying can generally reach or even several times more than the new product.
3. Thermal spraying technology future development trend and outlook
From the future development trend, the research of thermal spraying system engineering will receive more and more attention. At present, many countries have strengthened the research on thermal spray system engineering, that is, starting from the failure analysis, through the surface pretreatment, spraying equipment, spraying materials and spraying process optimisation, to develop a thermal spraying implementation process plan. In the process of development, thermal spray technology and other disciplines cross-pollinate to form a new surface treatment process. Future thermal spraying technology may be developed in the following aspects:
(1) in the choice of coating materials: flame spraying technology, plasma spraying technology and supersonic flame spraying technology used in the powder-type coating materials will also be the mainstream of market demand, arc spraying technology and cold spraying technology spraying material selection, although there are certain limitations, but the future with the progress of the process and updating, but also will be further expanded.
(2) in the combination strength of the coating and the substrate: cold spraying, supersonic flame spraying, supersonic plasma spraying and LPPS-TF coating and other relatively high strength of the combination with the substrate, will play a greater role.
(3) In the research of basic theory: thermal spraying technology is a marginal discipline involving multiple disciplines and strong intersectionality. It is affected by high temperature, high speed and mechanical non-uniformity and other parametric factors, thermal spray technology basic theory research faces great difficulties, the basic theory of the research is particularly important.
(4) In the research and development of new spraying materials: the general development trend of thermal spraying materials is: the composite and low impurity coating composition, the structure of the ultra-micro and nano, and nano-structured composite, multi-alloys and other new materials for the development of research hot spots.
(5) in the spraying process and equipment research and development: to improve the coating quality and expand the key to the sprayed material is to improve the energy and speed of the sprayed particles, therefore, the improvement and development of thermal spraying process and equipment should be developed in the direction of high-energy and high-speed development.
(6) in the expansion of new applications: thermal spray technology and other disciplines with each other penetration, interlinked characteristics, the use of this feature of the continuous development of new thermal spray technology, and the development of new applications of thermal spray technology. The combination of thermal spray technology and other related technologies is an effective way to explore and develop new applications of thermal spray technology.
This article is excerpted from a note on the wechat public account "Powder Metallurgy and Cemented Carbide Exhibition".
Company product profile:
Luoyang Golden Egret Geotools Co.,Ltd. founded in2012,is wholly-owned by iisted company XiamenTungsten Co.,Ltd (XTC).As a backbone cemented carbideenterprise of XTC with registered capital of 1.05billionRMB and first investment of ibillion RMB,GEOTOOLSspecializes in producing and selling high quality tungstenpowder,Tungsten Carbide Powder, carbide anvils,carbideroll rings,carbidesubstrates for PDC bit,mining drill bitsand hard facing materials.
Based on decades of production experience of WC based hard-facing materials, world-class technologies and modernautomatic production lines, GEOTOOLS dedicates into development and production of high quality hard facing materialwith high hardness, best wear resistance, best corrosion resistance and application solutions.
XTC brand Thermal Spray Powder mainly includes Wc- based & Cr3C2-based. The WC coating has high hardnessdurable wear resistance, abrasion resistance, corrosion resistance and high bonding strength, mainly used in oil &gas valves, mining tools, injection screws and printing machinery parts, The Cr3c2 coating has higher thermalstability and anti-oxidation, which can be used in a high temperature and corrosive environment, e.g. inner- wall ogas pipeline and pump.
With high degree of sphericity & excellent alloy organization, cemented carbide pellet is mainly used in weldingas an additive material of PTA Powder and tubular weldina rod to improve the wear resistance of the work pieces.
GEOTOOLS provides mono-crvstalline WC-based, coarse-arain wC-based, casting WC-based and other kinds ofPTA powder. With the high quality material, most advanced production lines and word-class technologies, the PTAcoating has high hardness, durable wear resistance, high welding velocity, and low porosity characteristics. Mainlyused in Mining, Oil driling, agriculture machinery, and machining for welding and repairing.
The hard phase of GEOTOOLS tube rods is tunasten or its products with high wear resistance. Tubular welding rods aresuitable for flame brazing and widely used for surface strengthen for oil and mining drill bits.
Privacy statement: Your privacy is very important to Us. Our company promises not to disclose your personal information to any external company with out your explicit permission.
Fill in more information so that we can get in touch with you faster
Privacy statement: Your privacy is very important to Us. Our company promises not to disclose your personal information to any external company with out your explicit permission.